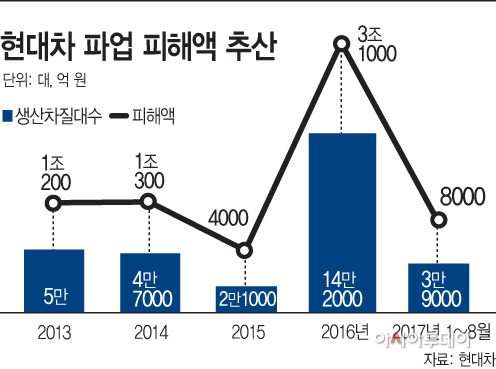 | | 1 | |
By AsiaToday reporter Kim Byeong-hoon
As Hyundai Motor's management and its labor union have temporarily suspended their wage and collective agreements, the interest is focused on whether the company will improve its industrial structure through mutual cooperation. Besides, the carmaker's subcontractors, who are failing to receive payments due to a sharp sales drop in China, are more likely to join the "China exit" by cutting off supplies. Experts say that the company should strengthen its global competitiveness by establishing a wage structure that enhances productivity, not a structure of low efficiency and high spending.
On Tuesday, AsiaToday analyzed the production disruption caused by the strikes of Hyundai Motor during the past five years and found that the company suffered 6.35 trillion won worth of loss in total. About 299,000 units of vehicles experienced delay in production. Operating profit, which represents profitability, is also declining every year. Although the company recorded the highest sales last year, its operating profit stood at 5.9 trillion won, the lowest level since 2010.
The union's unreasonable demands and strikes are an annual event for Hyundai Motor. The union has been striving to raise high wages through strikes. From 2011 to 2015, the Hyundai Motor union members' pay increased by an annual average of 5.1% while the rate of increase for those working for Volkswagen and Toyota was 3.3% and 2.5%, respectively. The average annual salary is 92.13 million won, surpassing Toyota (89.70 million won) and Volkswagen (83.96 million won). The ration of labor cost to sales was 13.09% for Hyundai Motor, which was much higher than Volkswagen (9.5%).
On the other hand, the productivity of Hyundai Motor is lower than other automakers despite its high wage structure. The hours per vehicle (HPV) of Hyundai Motor Company is 26.8 whereas the figure is 24.1 for Toyota and 23.4 for Volkswagen. There are warning signs ahead for the company both at home and abroad as it has been caught in a vicious circle where labor costs are increased due to rising wages and labor productivity is deteriorated due to frequent strikes.
Experts point out that Hyundai Motor needs fundamental improvement, such as improvement of cost structure through 'labor-management cooperation' in order to overcome such challenges. "Automakers that were involved in confrontational labor-management relations such as GM, Jaguar and Land Rover suffered from high cost and low efficiency, and eventually collapsed," said Kim Pil-soo, a professor of engineering at Daelim University College. "Establishing cooperative labor-management relations to secure jobs and ensure productivity will be a great driving force for Hyundai to overcome its crisis," he said.
In fact, the automakers, whose labor and management managed to reach a compromise, have successfully rebounded. Volkswagen posted an operating loss of more than 1 trillion won in 1993. Instead of dismissal, the company guaranteed employment of more than 100,000 workers and created jobs by expanding factories in the country. The union accepted a 20% reduction in working time and a cut in wages. As a result, Volkswagen succeeded in reducing costs by more than 1 trillion won a year without restructuring and improved its operating profit rate to 1.7% in 1998 from -8.7% in 1993.
Toyota also agreed to raise monthly base wages by 1,300 yen at the labor and management wage negotiations in March this year, when Volkswagen took the top spot for global car sales last year. This is 13% lower than the previous year's rise. Based on the experience of driving the company to a catastrophe through long-term labor dispute during the 1951 crisis, the labor union demanded job security instead of pay increase. The union's strategy was right. The company reduced the overseas transfer of factories, and increased production in Japan. Since 1962, the company's labor union has not staged any strikes.